The aircraft geometry is a combination of aluminium and 3D printed sections which provided significant cost and delivery benefits to the project. The framework supporting these components could be adapted to allow future testing with different aircraft models.
An existing AMT Olympus model engine has been modified to act as an air mover - so the combustion components were removed, and the blades are turned using a small compressed air supply which in turn draws ambient air through the intake. The back end was then replaced with a 3D printed section which was designed to replicate the exit trajectories of a fully deployed thrust reverser. The intention is to allow these rear end sections to be readily replaced to provide comparable data for different designs. |
The flight stream is provided by S & C's large scale Flight Stream rig. This is driven by two Gnome turboshaft rigs supplying compressed air to ejectors, which entrain large volumes of ambient air into a settling chamber. The working section was designed to supply a flight stream of 10-12m/s across the nose, fuselage, engine and active wing sections.
The thrust reverser plume and the flight stream can be independently controlled to replicate the interaction between the two opposing flows. This operation of multiple flows provides a full system test. |
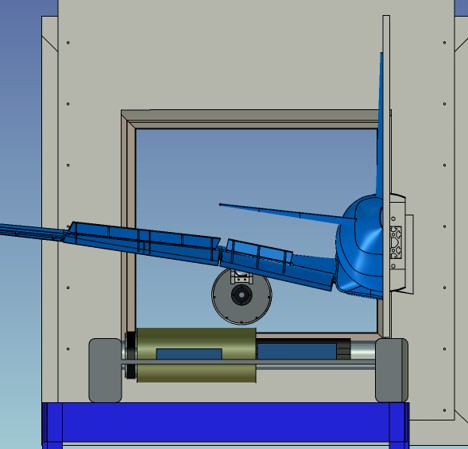
|
S & C Thermofluids operates a full pressure and temperature logging system and this is used to monitor the flow conditions in and around the simulated engine, and to investigate the locations where the plume impinged on the fuselage. Additionally, infrared imagery provided thermal data for the surfaces.
Visualisation techniques include smoke, water mist and thin strings. Future development will consider the use of a full combusting engine within the existing framework to more accurately capture the temperatures found in a landing scenario. This will also allow visibility of the exhaust plumes in the MW infrared imagery.
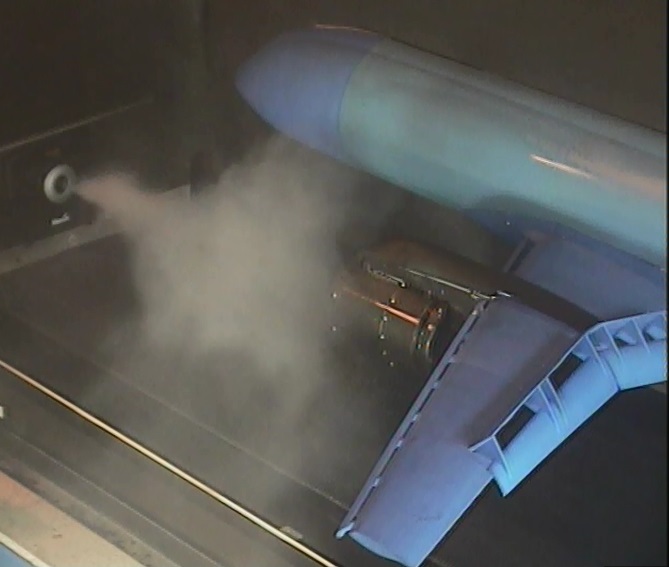
The rig was developed under SANTANA: System Advances in Nacelle Technology AerodyNAmics, an ATI R&T Programme funded project led by Bombardier Belfast.
|